Table of Content
These are applied at different rates depending on how deep you want them to go into the surface. If you want to remove a large amount of material, apply the chemicals for longer periods so that they can be as strong as possible. By repeatedly etching and re-imaging this way, engineers can create complex patterns for different components like memory chips and processors. The silicon nitride cpu is a silicon wafer that is based on a silicon wafer. These chips are made of a single silicon nitride, and have multiple transistors. One wafer can contain up to three million components.
A watt of power is equivalent to five gigawatts of power. So, how does a silicon wafer differ from a conventional chip? Using a wafer is also less expensive than a conventional CPU, which makes it more affordable.
What is a Silicon Wafer CPU?
Once cooled the silicon crystal seed is pulled from the crucible at a very slow rate of about 90mm per hour. Think of a semiconductor as something that can run hot and cold. Hot when conducting electricity and cold when insulating against it. After Carbon, Silicon is the second most ubiquitous material on earth.

Just watch the video and realize that all the electronics that he used didn't exist either in the quality or ease of use. Even then, I didn't catch if the materials used were even known to exist with this latest build. Silicon and metal are the two main components of each computer chip. A processor is made up of numerous transistors found on each chip. On a single chip, there may be tens of millions of transistors. The Z2 is also much more efficient compared to Zeloof's first design.
More from History-Computer
This means that a silicon chip made with a silicon wafer would cost around two hundred dollars. It would have to be fabricated in a factory, which takes time and patience. A fabricated chip would be made using a silicon wafer. If a silicon wafer chip costs more than two hundred dollars, it is more expensive to build. The packaging of the dies includes a substrate and a heat spreader, and they take on the recognizable shape of a desktop CPU. Heat is transferred from the silicon by the heat spreader into the heatsink positioned on top of it.
Silicon also has the great ability to be formed into wafers with a variety of thicknesses, which gives them the ability to be integrated on circuits. The different thicknesses allow researchers to create various semiconductor devices at different price points. Dust is a central concern for all Silicon circuit production.
Step 7: Electroplating
Also due to limited budget the results are a whole lot larger then modern techniques and I followed a similar approach as did the early pioneers of transistors. This is to be assembled in a spare room or garage where it is dark. Building this should only be attempted if you have knowledge of semiconductor manufacturing and know the proper safety precautions. The electrical conductivity of certain parts of the chip can also be altered by doping them with chemicals under heat and pressure. The manufacturing process of semiconductors is complicated. Integrated circuits can contain hundreds of millions and even billions of transistors.
Chip manufacturers first cut silicon wafers to the desired size to make a computer chip. The wafers are then polished and cleaned before any further processing can take place. Once they are cut, they undergo a series of processes that add layers of different materials to the surface of the die. These layers serve different purposes, such as creating electrical paths or isolating different regions of the chip.
The exposed areas of the photoresist are then developed, which creates openings in the resist that correspond to the desired pattern. The wafer is then etched, which transfers the pattern into the underlying substrate. When a silicon wafer is made, it is spun in a crucible. A small seed crystal is inserted and slowly drawn out of the molten silicon.
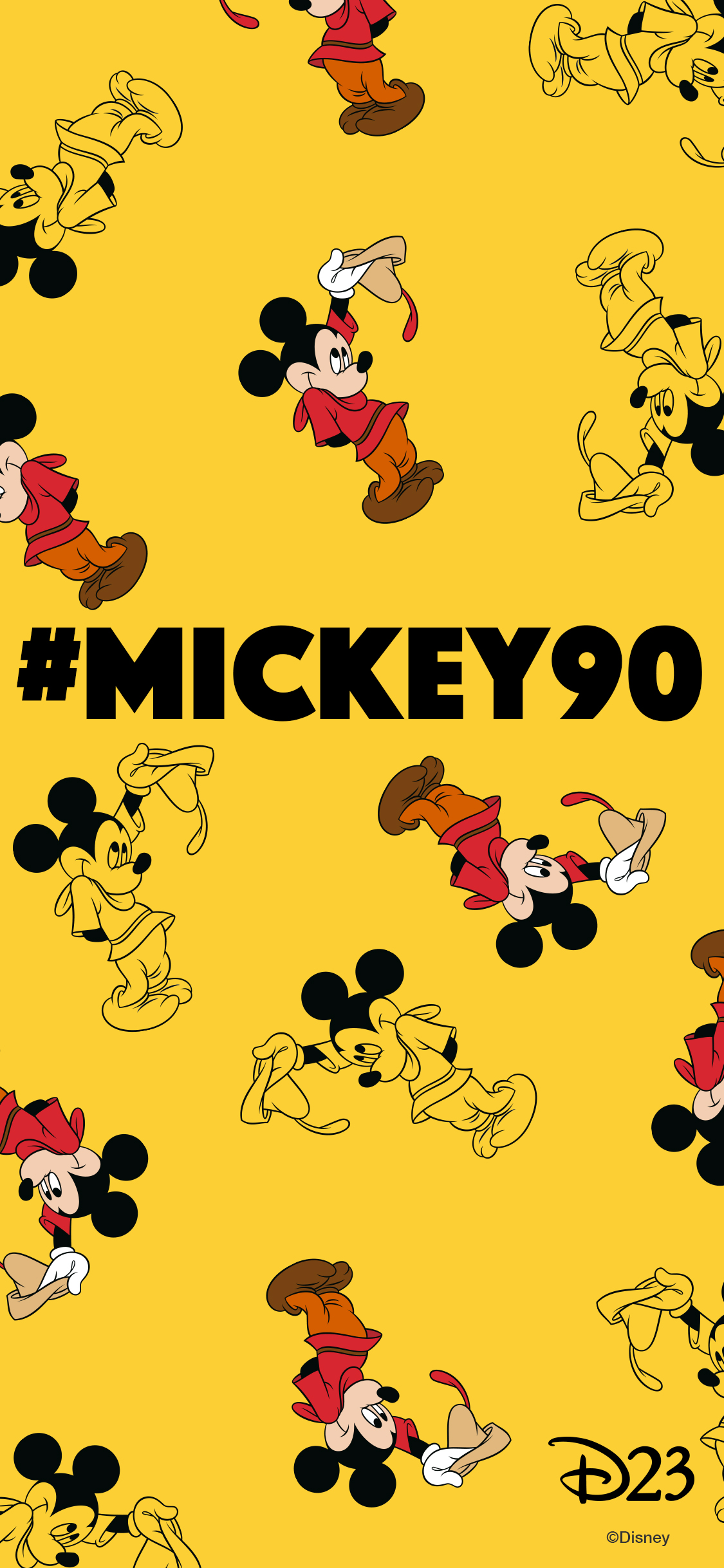
A computer chip is also known as an integrated circuit, and it is made up of semiconductor material. The most common type of semiconductor material used is silicon. Other materials used in making computer chips include germanium and gallium arsenide. These materials are used because they have special properties that make them good for making transistors. When you turn on a transistor by applying a voltage to its gate electrode, you cause electrons to flow from its source electrode to its drain electrode. A layer of photoresist is then spread thinly across the wafer.
When first learning about semiconductors and the silicon that fabricates them, many people wonder what does a silicon wafer look like. The pattern formed by the etching process is called a “mask,” and it’s what gives the chip its shape and functionality. The mask is made from photoresists, which are materials that can be chemically modified to make a pattern on a surface. The photoresist is exposed to ultraviolet light shined through a patterned plate, or "mask," which hardens the areas exposed to the light.
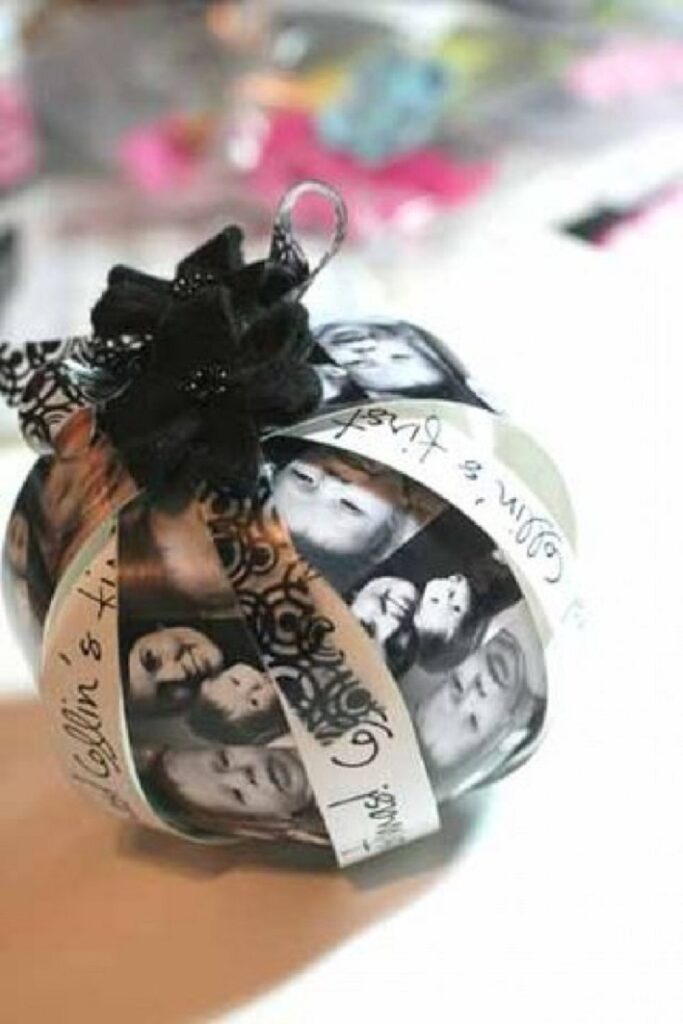
Hi everyone this is Matt H I am a college student studying Microelectronic Engineering . I wanted to apply what I learned and came up with the idea to make my own cleanroom to test experiments. This instructable covers how to build a cleanroom/cleanbox and preform photolithography, oxide growth, and etching at home. These steps are integral processes to how modern computer chips are made. Due to a limited budget instead of making a whole room into a cleanroom I had the idea of making a glovebox like design with modifications.
After that, processors are tested in terms of power use, maximum frequency, and other performance indicators. An insulator prevents any current from flowing until the transistor is turned on. Once turned on, the transistor acts like a conductor, allowing current to flow.
For comparison, Intel's 4004 CPU had 2200 transistors, while the Z2 has 1200 and is built on the same process. What took a whole company to do in the 1970s is now being done by a single person in his own home. Silicon is a gray color that changes with the amount of oxide grown.
The silicon wafers are then refined to provide the best surface for the fabrication of PC chips. Once the silicon is sufficiently refined, a layer of photoresist is applied to the surface of the silicon wafer. The photoresist becomes soluble and is washed away by solvent. After the photoresist is removed, a hard pattern is applied to the wafer.
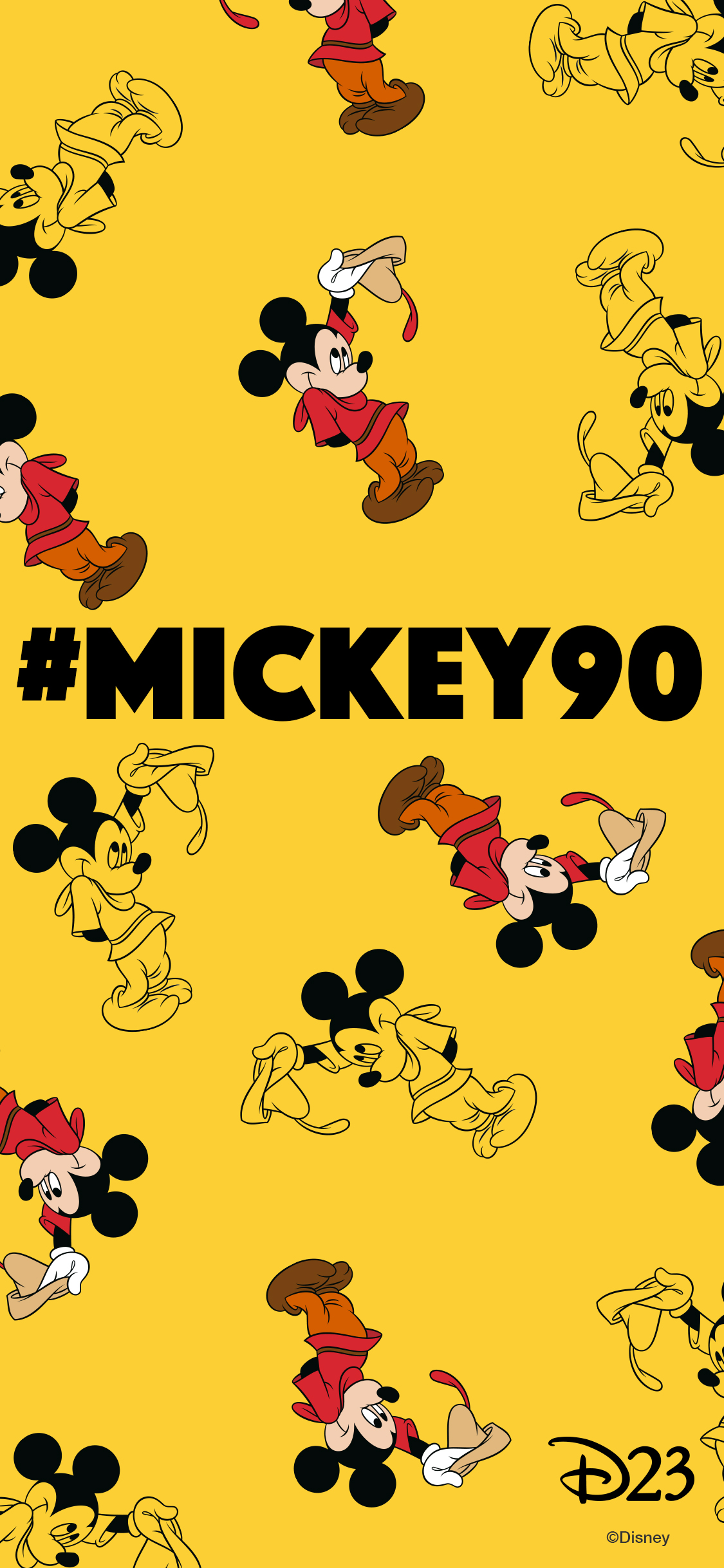
If no voltage is applied to the gate electrode, no current will flow. One important point about this process is that the gate electrode only turns off the current once it reaches its drain. It does not stop the current midway through the device. Very good for him to be interested and learning all this micro electronic stuff. But as for "a teenager building a chip in his garage", its missing the part about being very rich, with parents most probably already working in this field.
No comments:
Post a Comment